Share this
New Technical Briefing: Industrial Steam Sampling Best Practices
by Katie Reid on Thu, Sep 17, 2020 @ 14:09 PM
In a new technical briefing you'll learn about the most common errors in steam sampling and six keys to doing it right.
Industrial steam expert Kelly Paffel and Edmonton Valve energy guru Tristian McCallion delivered a 25-minute technical briefing on steam sampling in July. We've posted a recording of it, along with additional resources, here:

In July, Kelly Paffel and Tristian McCallion led a technical briefing, “Steam Sampling,” packed with practical advice grounded in decades of experience helping engineers, operators, and technicians optimize steam generation areas. We’ve posted the recorded briefing online, along with resources attendees downloaded after the session. All the resources are free.
Every boiler plant or steam generation area requires frequent testing. Checking boiler chemistry, boiler water quality, carry over, and condensate corrosion is essential. Operators monitor PH, conductivity, hardness, OH alkalinity, sulfites, and phosphates. They also monitor dissolved gases, particularly oxygen; and conduct other tests depending on chemical vendors' recommendations.
Paffel points out that, even in a basic steam system, operators need to take samples from about seven different points in the system. In a complex system, sample points may increase by a factor of two, three, or more.
Daily testing is best, and accurate results depend on numerous factors. It's wise to have a central location for sampling where you have the correct valves for positive shut off, double valve protection, cooling to below 90oF (32oC), discharge of samples to a safe location, and more.
Paffel and McCallion step through common errors like leakage, incorrect valves, lack of clear operating procedures, and improper labeling. Such problems result in inaccurate sampling and higher than necessary operating costs. Even worse, they can result in personnel being burned or injured in other ways.
Then they identify at least six keys to proper design, assembly, and installation. One is accounting for the way tubing and pipe expand when heated. If you have a 200-foot run of tube or pipe that goes from 50 to 650oF, McCallion explains, your design needs to account for six inches of expansion and contraction.
Another key is tapping lines in the right places. If they are too high, you'll be getting samples at the liquid/vapor interface or entirely from the vapor space, which means terribly inaccurate results.
Threads need special sealant and lubricant to handle high temperatures. Supports and brackets need to remain strong at high temps. Personnel should be shielded from hot pipes, tubes, hoses, valves and other components. Even instruments need to be suitable for high temperatures. (Gauges, for example, are generally limited to about 212oF (100oC) if they are liquid filled.)
Over the past 28 years, Paffel has personally conducted thousands of steam system audits, project management tasks, product design, engineering assignments and training sessions in the United States and overseas. He has achieved Steam System Level V certification in Steam Systems, is a member of the US Department of Energy’s (DOE) Steam Best Practices Committee and Steam Technical Committee, and has published many technical papers on steam and compressed air system design and operation.
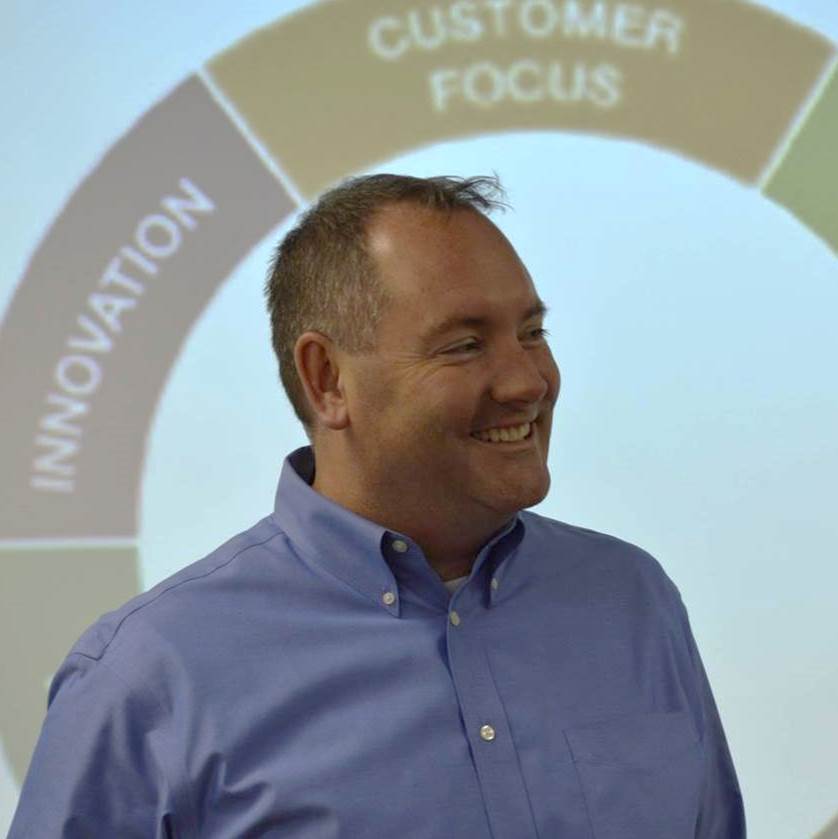
Edmonton Valve has relied on McCallion for 26 years. His current title is Custom Solutions Manager. Earlier, he supervised our sales team. Before that, he managed a sales territory in Edmonton and northeastern Alberta. For 12 years he also worked with Swagelok Energy Advisors across north America, providing training on steam fundamentals (TAP) , steam trap testing & worked on a number of different steam system audits.
View the full technical briefing and supporting resources here:
Steam system audits (now with RealWear headsets)
Whether you have a refinery, power plant, or other industrial operation, downtime in your boiler plant area costs big money. Even smaller problems --ones that don't halt production -- are a drain on resources.
Why put up with a problem when you don't have to? Our certified engineers can promptly examine your systems and identify concrete ways to boost consistency, reliability, and efficiency. And in 2020, to maximize speed and value delivered, they wear hands-free RealWear headsets while doing evaluations.
Share this
- Fittings (82)
- Cost Savings (70)
- Valves (67)
- Fabrication (59)
- Services (41)
- Videos (33)
- Steam Systems (29)
- Training (27)
- Downloads (25)
- Resources (25)
- Sampling (24)
- Tubing (24)
- Field Advisors (18)
- Hoses (12)
- Oil & Gas (10)
- Regulators (9)
- Winterization (9)
- Gas Distribution (7)
- Hydrogen & Clean Energy (4)
- About Us (2)
- Measurement (2)
- February 2025 (1)
- November 2024 (1)
- October 2024 (2)
- August 2024 (1)
- July 2024 (1)
- June 2024 (4)
- April 2024 (4)
- March 2024 (2)
- January 2024 (3)
- December 2023 (2)
- November 2023 (3)
- October 2023 (2)
- September 2023 (3)
- August 2023 (3)
- July 2023 (3)
- June 2023 (2)
- May 2023 (4)
- April 2023 (2)
- March 2023 (2)
- February 2023 (3)
- January 2023 (2)
- December 2022 (1)
- November 2022 (1)
- October 2022 (2)
- September 2022 (5)
- August 2022 (3)
- July 2022 (6)
- June 2022 (4)
- May 2022 (3)
- April 2022 (1)
- March 2022 (2)
- February 2022 (3)
- January 2022 (4)
- December 2021 (4)
- November 2021 (6)
- October 2021 (3)
- September 2021 (5)
- August 2021 (9)
- July 2021 (5)
- June 2021 (7)
- May 2021 (7)
- April 2021 (4)
- March 2021 (3)
- February 2021 (3)
- January 2021 (2)
- December 2020 (3)
- November 2020 (3)
- October 2020 (2)
- September 2020 (3)
- August 2020 (3)
- July 2020 (3)
- June 2020 (3)
- May 2020 (3)
- April 2020 (2)
- March 2020 (3)
- February 2020 (3)
- January 2020 (3)
- December 2019 (2)
- November 2019 (3)
- October 2019 (3)
- September 2019 (2)
- August 2019 (3)
- July 2019 (2)
- June 2019 (2)
- May 2019 (3)
- April 2019 (3)
- March 2019 (3)
- February 2019 (2)
- January 2019 (3)
- December 2018 (2)
- November 2018 (2)
- October 2018 (4)
- September 2018 (2)
- August 2018 (3)
- July 2018 (3)
- June 2018 (2)
- May 2018 (4)
- April 2018 (3)
- March 2018 (3)
- February 2018 (3)
- January 2018 (4)
- December 2017 (1)
- November 2017 (4)
- October 2017 (4)
- September 2017 (4)
- August 2017 (5)
- July 2017 (3)
- June 2017 (4)
- May 2017 (4)
- April 2017 (3)
- March 2017 (5)
- February 2017 (4)
- January 2017 (4)
- December 2016 (3)
- November 2016 (3)
- October 2016 (4)
- September 2016 (3)
- August 2016 (4)
- July 2016 (2)
- June 2016 (2)
- May 2016 (2)
- April 2016 (4)
- March 2016 (2)
- February 2016 (3)
- January 2016 (4)
- December 2015 (4)
- November 2015 (4)
- October 2015 (5)
- September 2015 (2)
- August 2015 (4)
- July 2015 (5)
- June 2015 (2)
- May 2015 (3)
- April 2015 (5)
- March 2015 (3)
- February 2015 (4)
- January 2015 (3)
- December 2014 (5)
- November 2014 (4)
- October 2014 (4)
- September 2014 (4)
- August 2014 (4)
- July 2014 (5)
- June 2014 (4)
- May 2014 (4)
- April 2014 (5)
- March 2014 (4)
- February 2014 (4)
- January 2014 (4)
- December 2013 (3)
- November 2013 (4)
- October 2013 (5)
- September 2013 (4)
- August 2013 (5)
- July 2013 (4)
- June 2013 (3)
- May 2013 (4)
- April 2013 (5)
- March 2013 (2)
- February 2013 (3)
- January 2013 (5)
- December 2012 (3)
- November 2012 (3)
- October 2012 (5)
- September 2012 (3)
- August 2012 (4)
- July 2012 (4)
- June 2012 (1)