Share this
New Technical Briefing: 2 Ways to Improve Refinery Pump Performance (+ 6 Free Resources)
by Katie Reid on Thu, Nov 19, 2020 @ 14:11 PM
Every minute of downtime matters and every dollar spent repairing systems count. The strategies outlined below can boost the energy efficiency of seal support systems—and take some pressure off of rotating equipment and reliability managers. Learn more and get a collection of free resources at our API 682 Seal Plans page.
Every petrochemical refinery would benefit from greater efficiency in its pumps, which are among the biggest consumers of energy. Any effort to improve pump efficiency helps reduce energy costs and extend pump life.
Mechanical seal support systems play a vital role in pump efficiency and reliability. Here are strategies to boost seal support systems’ energy efficiency throughout the plant:
1. Change the API plan
Mechanical seals operating in high-temperature fluids need cooling to improve the pressure margin over vapour pressure, prevent coking, or stay within temperature limits of secondary elastomeric seals.
One popular approach to cooling uses API Plan 21, which takes process fluid from the pump discharge, passes it through a cooler, then sends it into the seal chamber to maintain the appropriate environment. But the American Petroleum Institute's Standard 682 lists dozens of piping plans recommended for shaft sealing systems on centrifugal and rotary pumps.
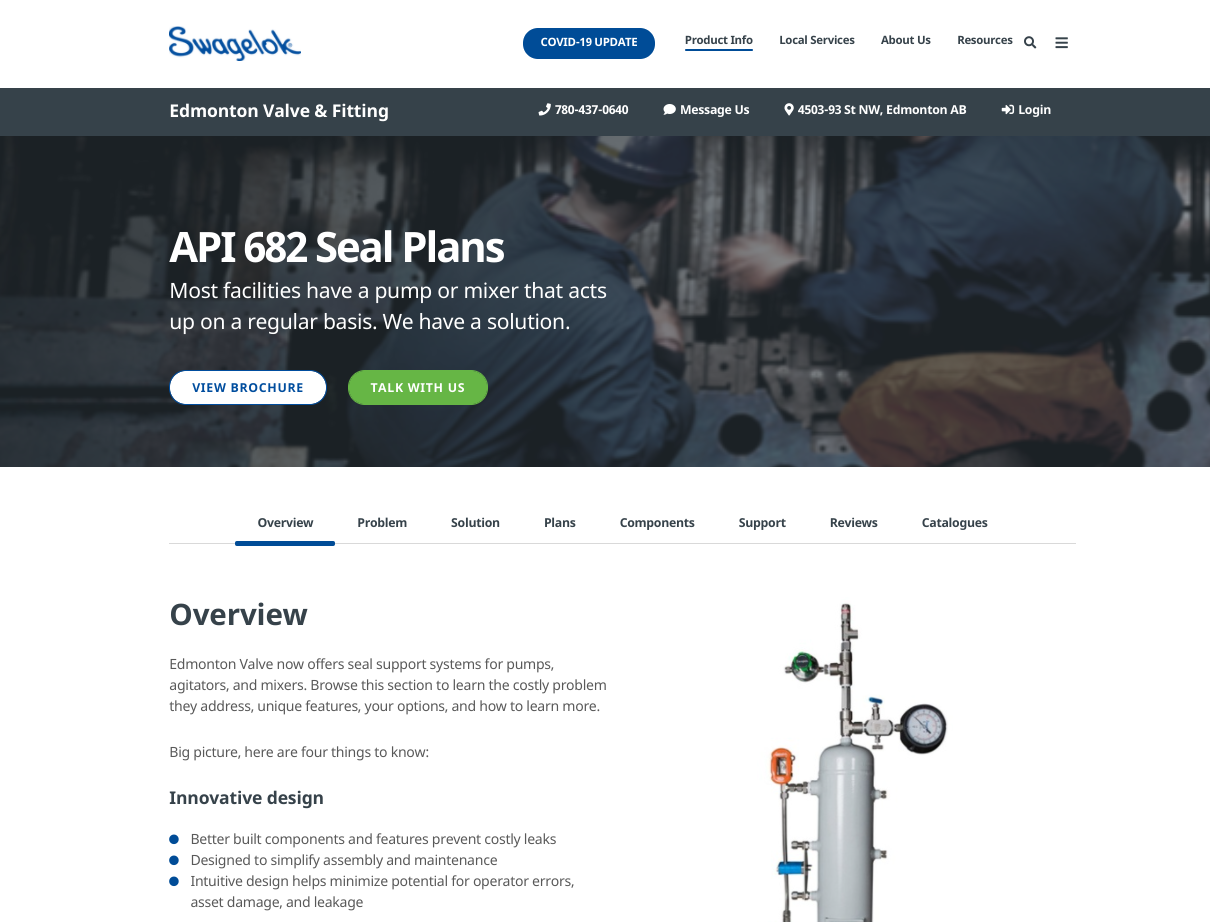
A more energy-efficient approach is API Plan 23. Instead of taking fluid from the process stream, API Plan 23 cools the seal chamber by recirculating the fluid from the cooler to the seal chamber and then back to the cooler. To accomplish this it uses an integrated pumping ring in the seal chamber. (For details see the Seal Plans page.)
With a reduced temperature differential in comparison to the process fluid, only the heat generated by the seal faces and seal chamber needs to be removed. This results in a more efficient cooling process and reduced energy consumption by the cooler.
Edmonton Valve & Fitting is glad to help develop a cost-benefit analysis for the feasibility of converting to API Plan 23. (To get that started, click the button above then click "Talk with us".) A detailed assessment should include your current cooling requirements, energy consumption, and annual costs compared with potential savings from an API Plan 23 configured to meet your unique cooling requirements. A change in plan will likely boost your seal support systems’ energy efficiency.
2. Upgrade seal system components
If any of your mechanical seals and support systems have been in place for years, consider an upgrade. Old components and systems may no longer be adequate. Consider replacing single seals with dual pressurized seals separated by a buffer or barrier fluid. This provides a more reliable separation between process fluids and the atmosphere, adding a safety margin against leakage of vapours in high-temperature or high-pressure environments.
API plans 52, 53, 54, 55, 72, and 74—and their variations—help ensure seals continue to operate efficiently and reliably.
Upgraded seal support system components also boost efficiency. Thermometers and pressure gauges connected to the instrumentation grid provide real-time monitoring of seal support system performance. An upgraded filter or cyclone separator may more efficiently remove fine particulates that degrade seal faces. Tubing promotes a more efficient flow of flush or cooling fluids than piping by eliminating joints prone to leakage. This also makes tubing an inherently cleaner upgrade from carbon steel piping covered in paint, rust, or hot dip zinc.
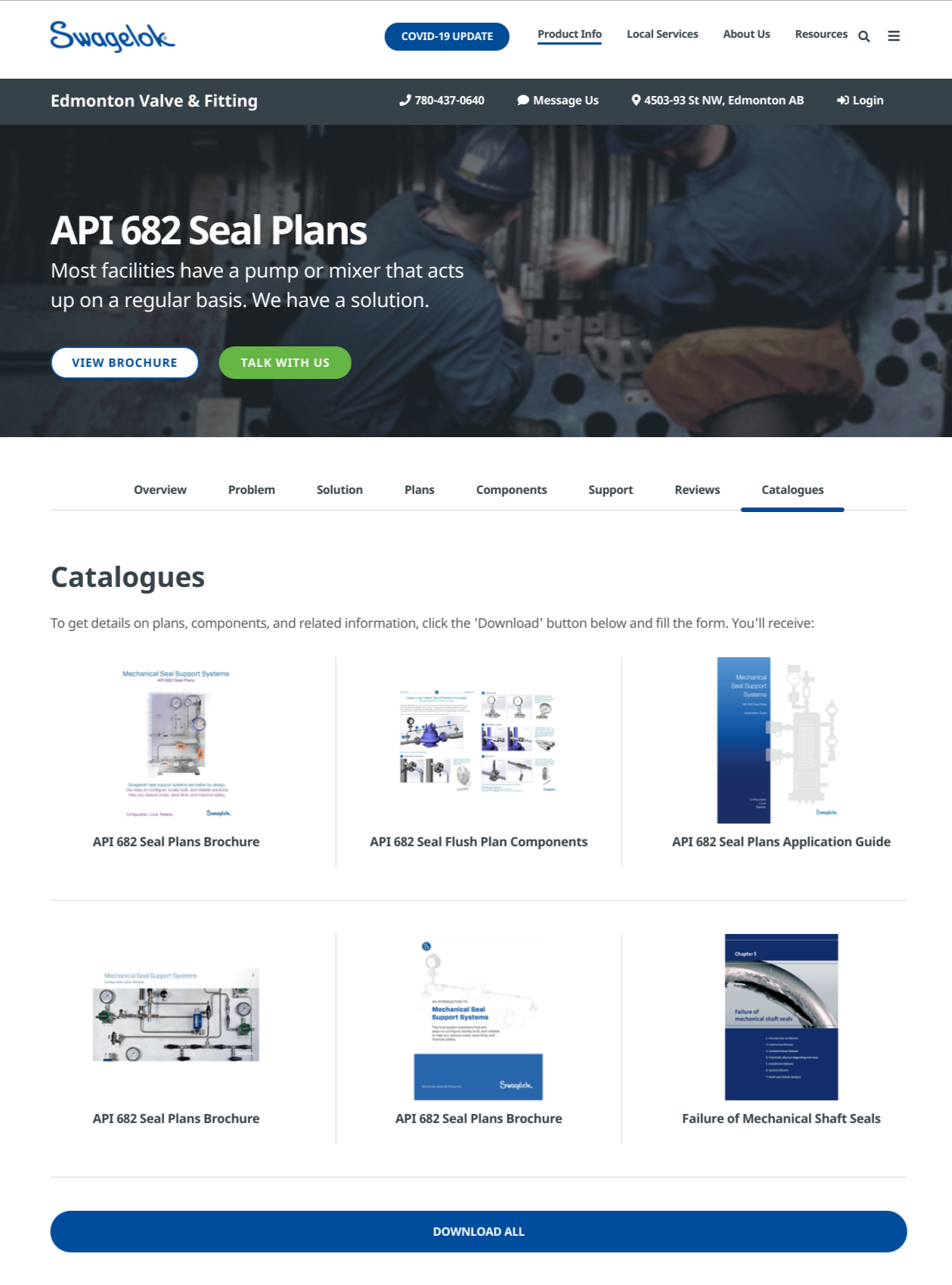
Identify other opportunities
If you’re responsible for improving energy efficiency and reducing unplanned downtime, you don't even have to build a seal support system to API specs. Edmonton Valve & Fitting can do it for you. We'll build your system right here in Edmonton—exactly how you want it and when you need it. For details, go to the Catalogues tab (pictured) of the API 682 seal plans page.
We can help you with a systematic review of your pump seals and seal support systems to identify opportunities for upgrades to provide a reliable seal chamber environment specifically tailored to current processing demands. We will take the time to produce a layout that works for you — maybe tall and skinny, maybe low and wide — so that you don't have an odd piece of equipment sticking out. Give us a call at 780-437-0640.
Share this
- Fittings (82)
- Cost Savings (70)
- Valves (67)
- Fabrication (59)
- Services (41)
- Videos (33)
- Steam Systems (29)
- Training (27)
- Downloads (25)
- Resources (25)
- Sampling (24)
- Tubing (24)
- Field Advisors (18)
- Hoses (12)
- Oil & Gas (10)
- Regulators (9)
- Winterization (9)
- Gas Distribution (7)
- Hydrogen & Clean Energy (4)
- About Us (2)
- Measurement (2)
- February 2025 (1)
- November 2024 (1)
- October 2024 (2)
- August 2024 (1)
- July 2024 (1)
- June 2024 (4)
- April 2024 (4)
- March 2024 (2)
- January 2024 (3)
- December 2023 (2)
- November 2023 (3)
- October 2023 (2)
- September 2023 (3)
- August 2023 (3)
- July 2023 (3)
- June 2023 (2)
- May 2023 (4)
- April 2023 (2)
- March 2023 (2)
- February 2023 (3)
- January 2023 (2)
- December 2022 (1)
- November 2022 (1)
- October 2022 (2)
- September 2022 (5)
- August 2022 (3)
- July 2022 (6)
- June 2022 (4)
- May 2022 (3)
- April 2022 (1)
- March 2022 (2)
- February 2022 (3)
- January 2022 (4)
- December 2021 (4)
- November 2021 (6)
- October 2021 (3)
- September 2021 (5)
- August 2021 (9)
- July 2021 (5)
- June 2021 (7)
- May 2021 (7)
- April 2021 (4)
- March 2021 (3)
- February 2021 (3)
- January 2021 (2)
- December 2020 (3)
- November 2020 (3)
- October 2020 (2)
- September 2020 (3)
- August 2020 (3)
- July 2020 (3)
- June 2020 (3)
- May 2020 (3)
- April 2020 (2)
- March 2020 (3)
- February 2020 (3)
- January 2020 (3)
- December 2019 (2)
- November 2019 (3)
- October 2019 (3)
- September 2019 (2)
- August 2019 (3)
- July 2019 (2)
- June 2019 (2)
- May 2019 (3)
- April 2019 (3)
- March 2019 (3)
- February 2019 (2)
- January 2019 (3)
- December 2018 (2)
- November 2018 (2)
- October 2018 (4)
- September 2018 (2)
- August 2018 (3)
- July 2018 (3)
- June 2018 (2)
- May 2018 (4)
- April 2018 (3)
- March 2018 (3)
- February 2018 (3)
- January 2018 (4)
- December 2017 (1)
- November 2017 (4)
- October 2017 (4)
- September 2017 (4)
- August 2017 (5)
- July 2017 (3)
- June 2017 (4)
- May 2017 (4)
- April 2017 (3)
- March 2017 (5)
- February 2017 (4)
- January 2017 (4)
- December 2016 (3)
- November 2016 (3)
- October 2016 (4)
- September 2016 (3)
- August 2016 (4)
- July 2016 (2)
- June 2016 (2)
- May 2016 (2)
- April 2016 (4)
- March 2016 (2)
- February 2016 (3)
- January 2016 (4)
- December 2015 (4)
- November 2015 (4)
- October 2015 (5)
- September 2015 (2)
- August 2015 (4)
- July 2015 (5)
- June 2015 (2)
- May 2015 (3)
- April 2015 (5)
- March 2015 (3)
- February 2015 (4)
- January 2015 (3)
- December 2014 (5)
- November 2014 (4)
- October 2014 (4)
- September 2014 (4)
- August 2014 (4)
- July 2014 (5)
- June 2014 (4)
- May 2014 (4)
- April 2014 (5)
- March 2014 (4)
- February 2014 (4)
- January 2014 (4)
- December 2013 (3)
- November 2013 (4)
- October 2013 (5)
- September 2013 (4)
- August 2013 (5)
- July 2013 (4)
- June 2013 (3)
- May 2013 (4)
- April 2013 (5)
- March 2013 (2)
- February 2013 (3)
- January 2013 (5)
- December 2012 (3)
- November 2012 (3)
- October 2012 (5)
- September 2012 (3)
- August 2012 (4)
- July 2012 (4)
- June 2012 (1)